Showing 1–9 of 11 results
Check valves offer essential flow control, preventing backflow to protect your systems and maintain efficiency. Designed for durability, check valves allow fluid to flow in one direction, keeping contaminants out and ensuring seamless operation across water, oil, and gas applications. Whether for home plumbing, industrial use, or commercial systems, check valves provide peace of mind by stopping unwanted flow and preventing costly damage. Experience the reliability and efficiency of check valves built to last.
Filter by Materials
- Alloy Steel (1)
- Brass (2)
- Carbon Steel (2)
- Cast Iron + Epoxy (7)
- Cast steel (2)
- Ductile iron + Epoxy (3)
- EPDM (1)
- PP (1)
- PVC (3)
- PVC-C (5)
- PVC-U (3)
- PVDF (1)
- Stainless Steel (9)
Filter by Diameter
- DN 10 - 3/8" inch (2)
- DN 750 – 30" inch (2)
- DN 900 – 36" inch (2)
- DN100 - 4" inch (11)
- DN125 - 5" inch (8)
- DN15 - 1/2" inch (6)
- DN150 - 6" inch (8)
- DN20 - 3/4" inch (5)
- DN200 - 8" inch (8)
- DN25 - 1" inch (7)
- DN25 - DN1000 (1)
- DN250 - 10" inch (6)
- DN300 - 12" inch (6)
- DN32 - 1 1/4" inch (5)
- DN350 - 14" inch (4)
- DN40 - 1 1/2" inch (6)
- DN400 - 16" inch (4)
- DN50 - 2" inch (10)
- DN50 - DN1200 (1)
- DN50 - DN2000 (1)
- DN500 – 20" inch (5)
- DN600 – 24" inch (5)
- DN65 - 2 1/2" inch (10)
- DN80 - 3" inch (11)
- DN80 - DN2400 (1)
Filter by
- Flange PN10 (6)
- Flange PN16 (10)
- Flange PN25 (3)
- Flanged ANSI 150 (1)
- Flanged PN10 (5)
- Flanged PN25 (2)
- Socket (3)
- Threaded (3)
Four Different Types of Check Valves
Check valves come in various designs, each suited for specific applications. Ball check valves feature a spring-loaded ball that seals against a conical seat, providing a simple and cost-effective solution for preventing backflow in liquid and gas systems. These valves are durable, self-cleaning, and work well under high pressure. Swing check valves operate through a disc that swings open with forward flow and closes when flow reverses. They’re ideal for large pipelines but can suffer from water hammer in high-flow systems. Lift check valves use a pressure differential to lift a disc or ball, allowing fluid to pass; these valves are well-suited for high-pressure, high-temperature applications where backflow prevention is critical. Finally, wafer check valves offer a compact, lightweight option designed for tight spaces, featuring a quick-response disc that prevents backflow with minimal pressure drop, making them perfect for industries like water treatment and chemical processing.
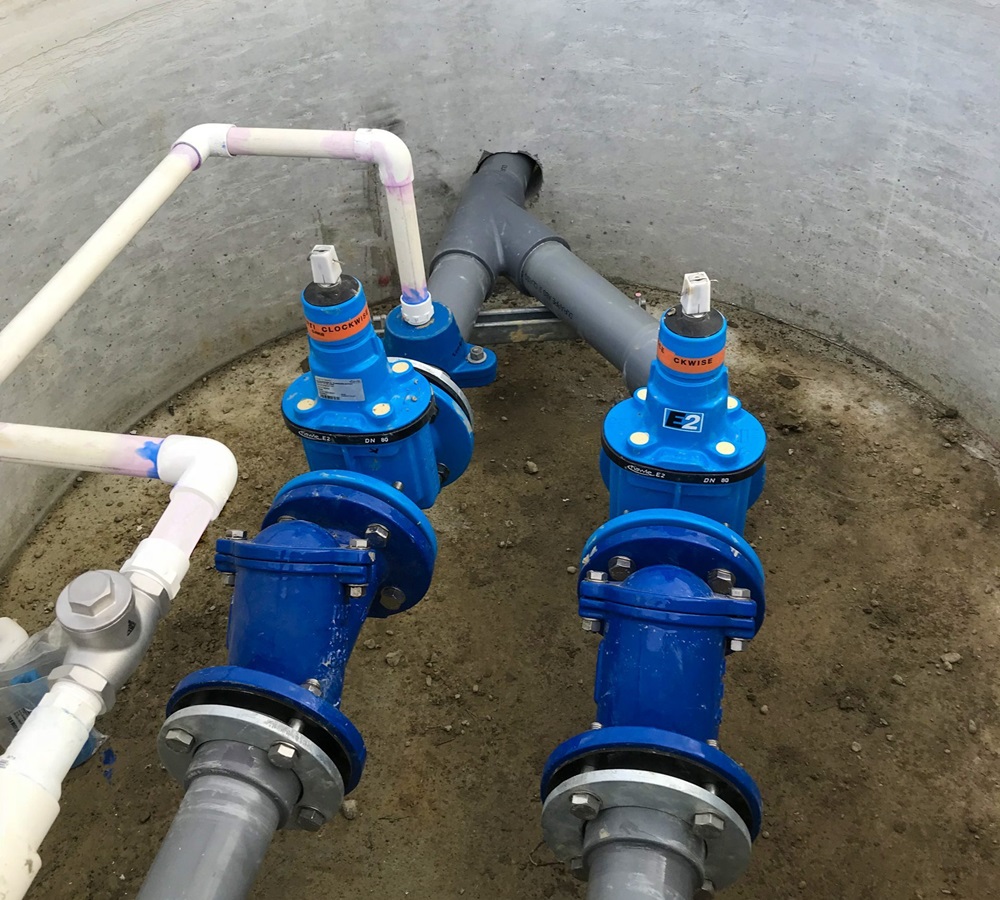
Ball Check Valve
Ball check valves are a versatile and reliable option for preventing backflow in various fluid systems. Their design features a spring-loaded or free-moving ball that creates a positive seal by blocking reverse flow when the pressure decreases. These valves are compact, easy to install, and cost-effective, making them a popular choice for smaller systems like pumps, dispensers, and air compressors. Suitable for both horizontal and vertical installations, ball check valves handle high-pressure applications and ensure long-lasting performance with minimal maintenance.
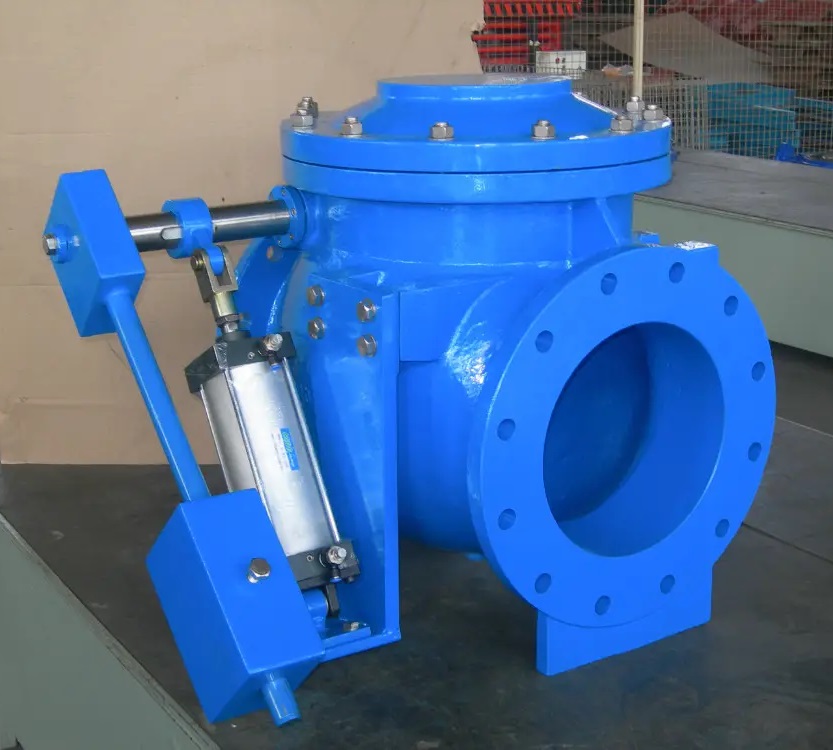
Swing Check Valve
Swing check valves are an ideal solution for larger fluid systems requiring efficient backflow prevention. They use a disc that swings open with forward flow and automatically closes when the flow reverses. Known for their durability, swing check valves are commonly used in high-volume pipelines, gas transmission, and wastewater systems. Designed for both vertical and horizontal installations, they offer reliable performance in various industrial environments. With their robust construction and ability to handle fluctuating pressures, swing check valves ensure smooth operation in demanding applications.
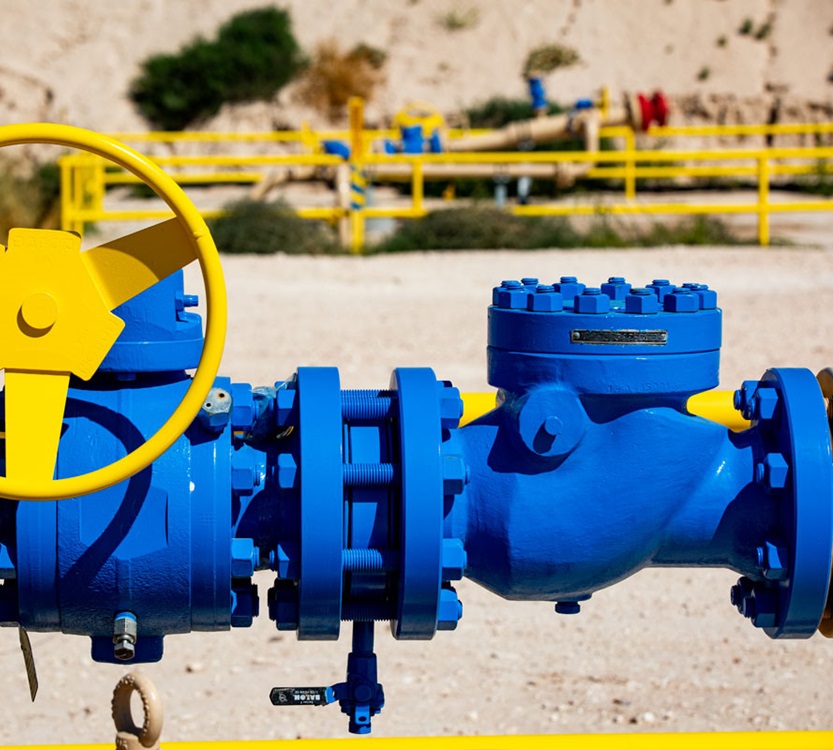
Lift Check Valve
Lift check valves are specifically engineered for high-pressure and high-temperature systems. They operate by lifting a disc or ball when there’s sufficient upstream pressure, allowing fluid to pass through. Once the pressure drops, the valve closes, preventing reverse flow. Lift check valves are commonly found in industries like chemical processing, power generation, and boiler systems, where maintaining system integrity is crucial. Their simple yet effective design makes them a dependable option for safeguarding equipment against backflow and contamination.
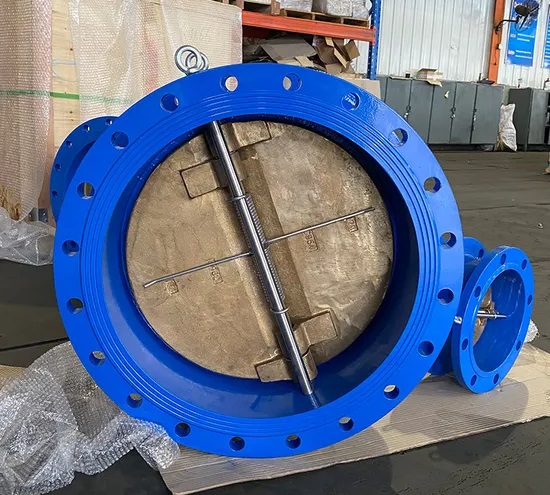
Wafer Check Valve
Wafer check valves are known for their compact and lightweight design, making them the go-to solution for systems with space constraints. They use a disc mechanism to allow one-way flow and prevent backflow when the flow reverses. Wafer check valves are easy to install between flanges and offer quick response times with minimal pressure loss. Suitable for water treatment, chemical processing, and HVAC systems, these valves are efficient and highly durable, ensuring reliable performance in various industrial applications.
What is the function of a check valve?
The primary function of a check valve is to allow fluid—whether liquid or gas—to flow in one direction while preventing reverse flow, ensuring the integrity of the system. This automatic mechanism plays a crucial role in preventing backflow, which could lead to contamination, equipment damage, or operational inefficiencies. Check valves are commonly used in industries like water treatment, chemical processing, and HVAC systems, where they protect pumps, compressors, and pipelines from pressure surges or reverse flow. By relying on pressure differentials to operate, check valves help maintain consistent flow without the need for external control or monitoring. They also enhance the safety and efficiency of fluid systems, ensuring smooth operation and reducing the risk of costly downtime or damage.
Check valve vs non return valve
While both check valves and gate valves are essential in controlling fluid flow, their functions and applications differ significantly. A check valve operates automatically, allowing fluid to flow in one direction and preventing reverse flow without any manual intervention. This makes check valves ideal for systems where backflow prevention is crucial, such as in water treatment and chemical processing. They rely on pressure differentials to operate and require minimal maintenance.
On the other hand, gate valves are manually operated and primarily used to start or stop the flow of fluid. By lifting a gate, they provide a full, unobstructed flow path when open and a complete shut-off when closed. Gate valves are typically used in larger pipelines, such as in water supply systems, where precise flow control is less critical, and full flow or complete shut-off is required. Unlike check valves, gate valves should not be used for regulating flow, as partial openings can lead to gate wear and reduced lifespan.
FAQs for Check Valves
A check valve is a mechanical device that allows fluid to flow in one direction only, preventing backflow. It operates automatically, without the need for manual intervention. The valve opens when fluid pressure from the inlet side exceeds the cracking pressure, allowing the fluid to pass through. When the pressure drops or reverses, the valve closes, stopping reverse flow. Check valves are commonly used in water treatment, chemical processing, and HVAC systems to protect equipment from damage caused by backflow.
Cracking pressure is the minimum pressure difference between the inlet and outlet of a check valve that is required to open the valve and allow fluid flow. Different check valves are designed for specific cracking pressures, which ensures that the valve opens only when necessary. This feature helps in preventing leaks or trickle flows. It’s important to select a check valve with the correct cracking pressure for your system to ensure optimal performance.
A ball check valve uses a spring-loaded or free-moving ball to block reverse flow, providing a simple, compact solution for smaller systems. It’s self-cleaning and effective for high-pressure applications. A swing check valve, on the other hand, uses a disc that swings open with forward flow and closes when flow reverses. Swing check valves are ideal for larger pipelines and high-volume systems. Both types are effective for preventing backflow, but their design and applications differ.
Check valves offer several key benefits, including the prevention of backflow, which protects systems from contamination or damage. They are automatic, requiring no manual operation, and are low-maintenance. Check valves also work well under variable pressure conditions, making them versatile for a wide range of industries such as water, oil, gas, and chemical processing. Additionally, their compact design allows them to be used in both horizontal and vertical pipelines.
Yes, many check valves can be installed in both horizontal and vertical orientations. For instance, ball check valves are versatile and can be placed in either direction, while wafer check valves are designed to be installed between flanges, making them suitable for compact spaces. However, it's crucial to check the valve’s specifications, as some models may require specific installation orientations to ensure proper function and prevent backflow.