Showing the single result
Gate valves deliver solid, reliable shut-off control, ideal for isolating fluid flow in residential, commercial, and industrial systems. Designed for durability and tight sealing, gate valves provide complete flow control with minimal pressure drop, making them perfect for water, oil, and gas applications. With a smooth, low-maintenance operation, gate valves offer long-lasting performance you can trust, even under high-pressure conditions. Ensure your system’s efficiency and prevent unwanted flow with this essential control solution.
What are the different types of gate valve?
Gate valves come in various types, each tailored to specific industrial applications, offering unique features that enhance performance and reliability. These valves are primarily designed to control the flow of liquids or gases by raising or lowering a gate within the valve body, ensuring minimal flow resistance when fully open and a tight seal when fully closed. The most common types of gate valves are categorized based on their design and material composition, which determine their suitability for different pressure, temperature, and fluid types. Some are optimized for high-pressure environments, while others excel in corrosive or chemical-rich conditions, ensuring long-lasting operation under extreme industrial demands. Gate valves are highly valued for their versatility across industries such as water supply, oil and gas, and manufacturing, where efficient flow control is critical. Each type of gate valve is engineered to meet specific operating parameters, such as pressure ratings, temperature tolerances, and compliance with standards like ISO. Next, we will introduce four common gate valve products in detail, providing an in-depth look at each to help you make informed decisions. Whether you need a valve for a high-pressure application or one that offers superior corrosion resistance, the range of gate valves available ensures you can find a solution tailored to your system’s needs. Understanding the different types of gate valves and their features allows industries to select the right valve, reducing maintenance costs and enhancing operational efficiency without compromising performance or safety.
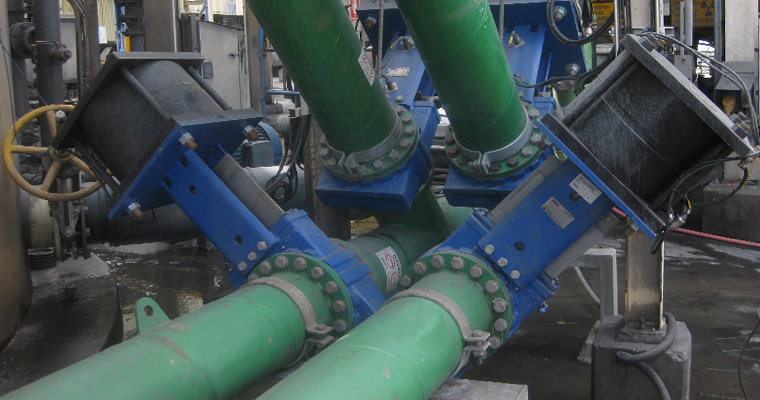
knife gate valve
The knife gate valve is specifically designed for handling thick fluids, slurries, and media with suspended solids. Its sharp-edged gate slices through dense materials, ensuring a full and secure closure even in challenging conditions. Commonly used in wastewater treatment, mining, and pulp industries, this valve excels in preventing clogging while ensuring reliable performance. Its low-maintenance design and cost-effectiveness make it an ideal choice for applications where solid-laden fluids are present. For industries looking for efficient flow control in demanding environments, knife gate valves are a trusted solution, providing long-lasting durability and operational efficiency.

pvc gate valve
PVC gate valves are a lightweight, corrosion-resistant option that excels in low to medium pressure environments. Ideal for applications where chemical exposure or moisture is a concern, such as irrigation systems or residential plumbing, these valves offer excellent chemical resistance and cost-effectiveness. PVC gate valves are easy to install and maintain, making them a reliable choice for systems that require a smooth, continuous flow without the risk of corrosion. Whether you need an affordable solution for fluid control in industrial settings or residential applications, PVC gate valves are a practical and durable option.
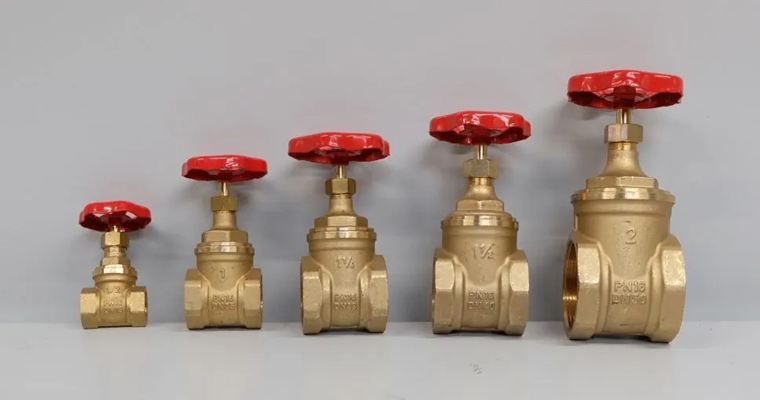
brass gate valve
Brass gate valves are highly regarded for their durability and excellent corrosion resistance, making them a preferred option for plumbing, heating, and gas systems. Constructed from high-quality brass, these valves provide superior strength and are capable of withstanding both high pressure and temperature environments. They offer reliable on/off flow control, ensuring a tight seal and preventing leakage in critical systems. With easy maintenance and long service life, brass gate valves are a cost-effective solution for fluid control in residential and commercial applications, delivering both performance and reliability.
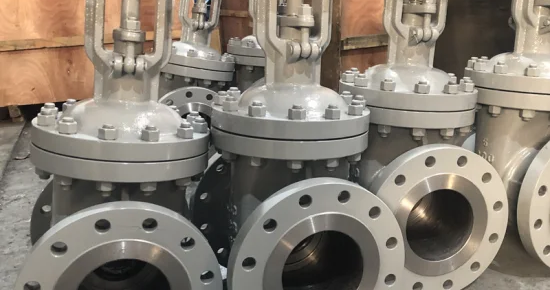
stainless steel gate valve
Known for its high corrosion resistance and ability to handle extreme temperatures, the stainless steel gate valve is essential in industries like chemical processing, oil and gas, and food production. These valves provide a secure seal in harsh environments and are designed to prevent contamination while handling high-pressure systems with ease. With their durable construction and low maintenance needs, stainless steel gate valves offer long-lasting performance in the most demanding industrial applications. If your operation requires reliable and contamination-free flow control, stainless steel gate valves are the industry-leading choice.
Gate Valve VS Globe Valve
Gate valves and globe valves serve different but crucial roles in industrial fluid control, each with distinct advantages. Gate valves, ideal for on/off control, allow full fluid flow or complete isolation, making them perfect for applications like pipelines where minimal flow restriction is essential. In contrast, globe valves excel in regulating flow, offering precise control in systems where throttling is necessary, but they create higher pressure drops due to their design. Gate valves, operating with a linear gate mechanism, minimize flow turbulence, ensuring durability in high-pressure environments. Globe valves, with their plug-like disc, are better suited for applications needing adjustable flow rates. When deciding between the two, consider the operational needs: gate valves are best for systems requiring a tight seal and full flow, while globe valves shine in scenarios needing flow regulation. With both valves offering unique benefits, choosing the right one depends on specific system requirements, such as pressure and flow control. Discover how incorporating the correct valve type can enhance operational efficiency while meeting your industry’s stringent demands for reliability and performance.
FAQs for Gate Valves
Gate valves operate using a simple yet highly effective mechanism. The valve's gate or disc moves up and down in a straight line to either block or allow fluid flow through the pipeline. When fully raised, the gate permits an unobstructed flow, ideal for systems requiring full on/off control, such as pipelines for isolation purposes. The straightforward design minimizes flow restriction and pressure drop, making gate valves a preferred choice for water supply, oil and gas, and manufacturing industries. By understanding how gate valves work, you ensure optimal performance and reduced operational costs.
Gate valves offer several key advantages, including their ability to provide a tight seal when fully closed, ensuring minimal leakage. This feature makes them ideal for critical applications like fluid containment in high-pressure systems. Additionally, gate valves allow for efficient, unobstructed fluid flow when open, reducing pressure drop and enhancing operational efficiency. Their durability and long service life, even under extreme conditions such as high temperatures and pressures, make them a reliable option across various industries, from chemical processing to water distribution. These benefits highlight why gate valves are an industry-proven solution for many fluid control needs.
Proper maintenance of gate valves is crucial to ensuring their longevity and performance. It's recommended that the valve be inspected and cycled regularly—at least once a month—to prevent sticking or jamming. Checking for signs of wear, corrosion, or debris in the valve seat is vital for preventing leaks and ensuring a tight seal. Lubricating the stem and cleaning the valve to remove any accumulated debris are also important steps. With regular maintenance, gate valves can deliver consistent performance, minimizing the risk of downtime and expensive repairs.
One of the most common issues with gate valves is debris or foreign objects obstructing the valve seat, which can prevent the valve from fully closing. To resolve this, the valve can be slightly opened to flush out contaminants with high-velocity fluid. If the valve fails to close properly or leaks, inspecting the gate and seat for wear or damage is essential. In cases where the valve becomes stuck in a partially open position, this is often due to over-torquing or actuator failure. Following these troubleshooting steps can help ensure smooth operation and extend the valve's service life.
To ensure optimal performance and avoid common installation issues, it's important to follow best practices when installing gate valves. This includes verifying that the valve's material and disc are compatible with the system's pressure and temperature requirements. Proper alignment of the valve with the piping or flange is crucial to preventing leaks and premature wear. After installation, cycling the valve several times to check for smooth operation and potential leakage will ensure long-term reliability. By adhering to these guidelines, you can enhance the efficiency and lifespan of your gate valves.